by Kelly Driver, MBA
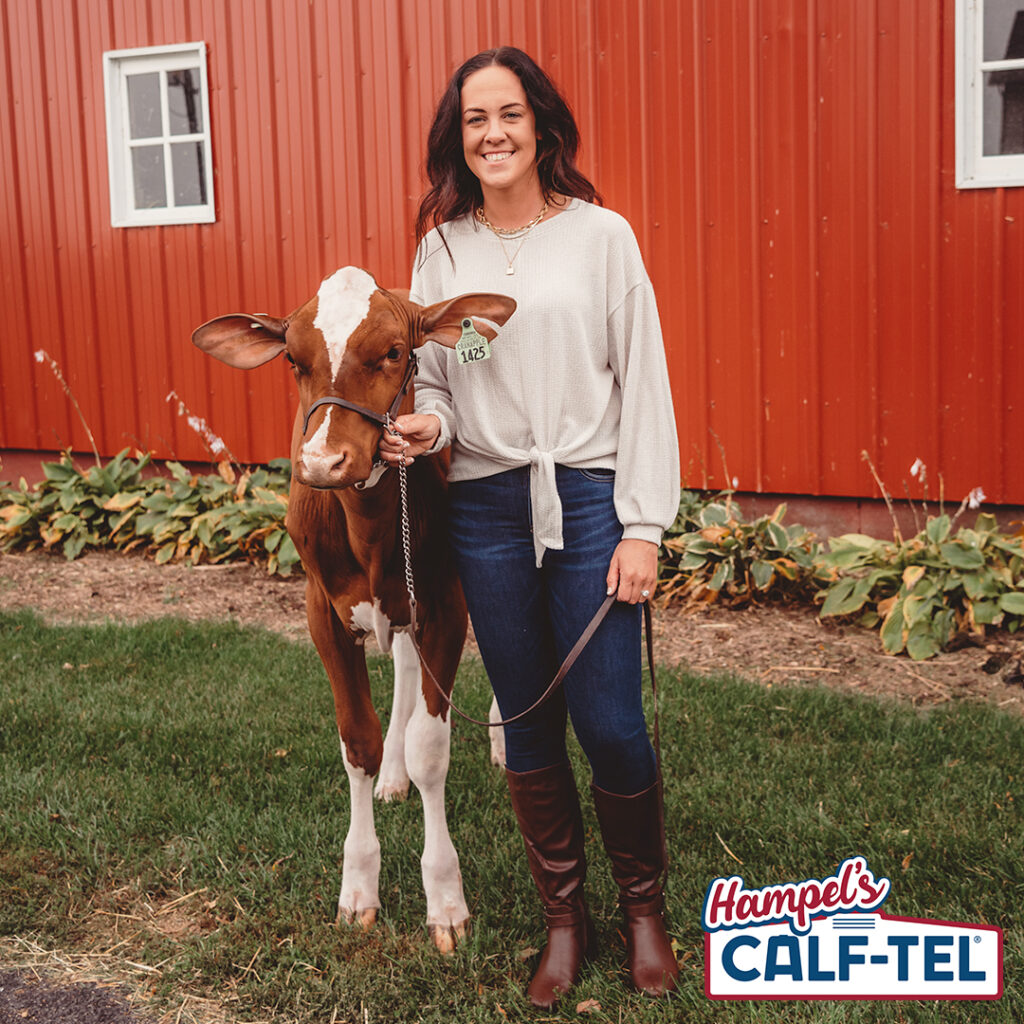
Junction City, WI
400 Pre-Weaned Calves
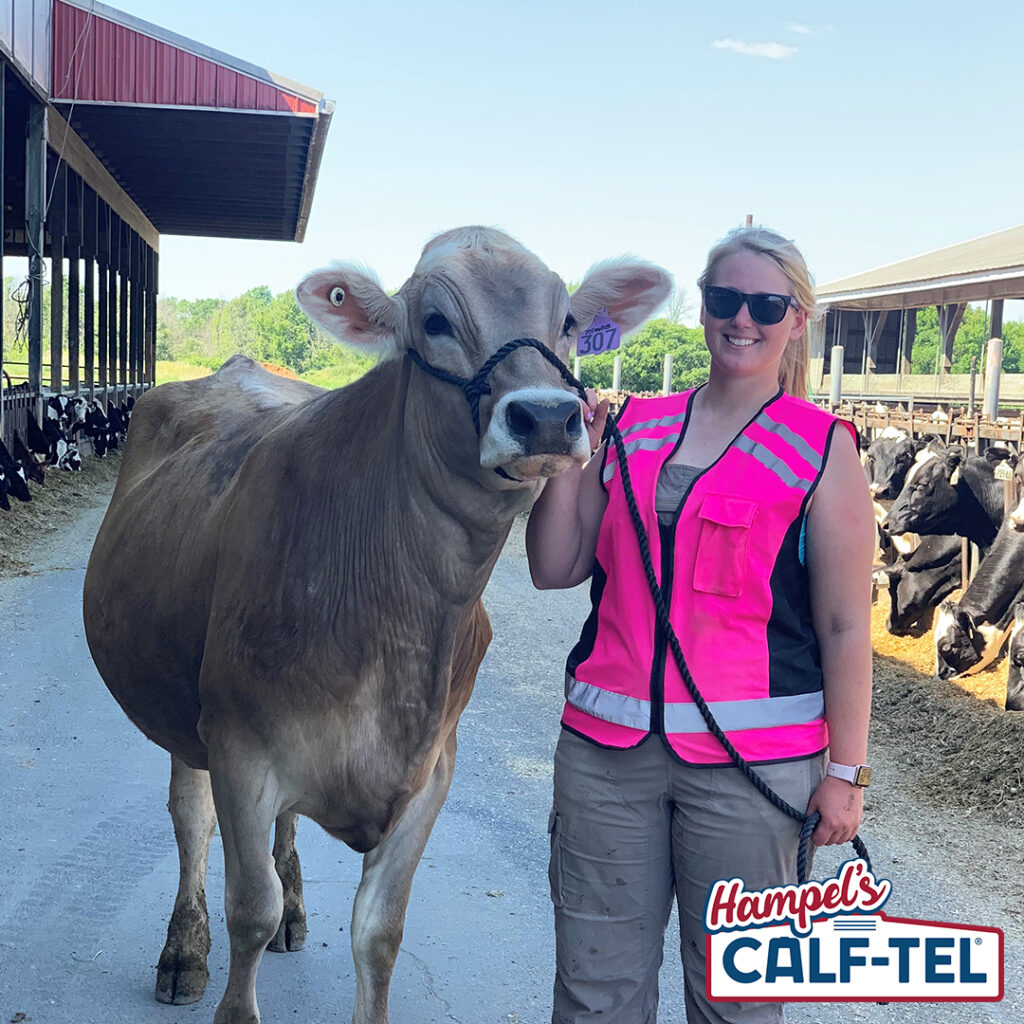
Clifton Springs, NY
600 Pre-Weaned Calves
When we consider calf care, we generally focus on things like colostrum, consistency and cleanliness, but how often do we consider another ‘C’ word of great importance – communication? This month we will hear from two skilled managers, of both calves and their calf care teams.
Please tell us a little bit about yourself.
RACHEL: I am currently the Dairy Operations Manager at Willow Bend Farm, LLC. My career started at Willow Bend Farm 10 years ago. Throughout that time, I have taken on many opportunities, ranging from working in different areas of the dairy, taking management courses and networking in the dairy industry.
MEGAN: I am the farm manager at Genetic Futures. While I did not grow up on a farm, I did spend lots of my time on my family’s farm, Erbacres Holsteins, and showing dairy cattle. I attended UW-Madison and obtained a degree in Dairy Science and have been working at Genetic Futures for 5 years.
Please tell us a bit about your operation.
RACHEL: Willow Bend Farm, LLC is a 4500 Cow Dairy in the Finger Lakes region of NY. We milk at three facilities, all within 30 miles of each other. We have 4100 head of young stock, and all our wet calves are raised at the home farm. We feed 600 pre-weaned calves in hutches, three times each day.
MEGAN: Genetic Futures is a recipient facility in Wisconsin, owned by Mike and Julie Duckett, where the end goal is to produce a healthy calf for our customers. We put a strong emphasis on calf care as we are raising some of the most elite genomic animals in the breed. We raise our calves in both hutches and calf barns. We have around 400 calves on milk at a time and they are fed bottles the entire time they are on milk. We feed calves 3 times a day.
Please tell us about the team you lead.
RACHEL: The calf team is made up of a total of 5 full time employees. 4 working on the day shift and one at night. This team also cares for the maternity area.
MEGAN: I lead a team of 4 people during the day and we do the morning and afternoon calf feeding as well as take care of bedding, cleaning, etc. Then the milking team does the night feeding.
How would you describe your leadership or management style?
RACHEL: Visionary, Leads by inspiring.
MEGAN: I would describe my management style as involved, as I enjoy being hands on with the calves and working closely with my team members. I would also say that it is performance focused as I strive to produce the best calf possible for our customers and I push my team to do the same. Finally, I would say that it is protective as I fight hard for my team and do the best I can to make it worth their time to be here and do a good job.
How do you recruit members of your calf care team and what qualities do you look for in team members?
RACHEL: We love to grow our people within the farm. Becoming a part of the calf team is a part of climbing the ladder. Rarely do we hire outside of the farm when it comes to working with young stock. It gives our employees something to strive towards. We look for our 5-core values in potential calf team members: Safety, Teamwork, Professional, Can-do attitude, and Positivity.
MEGAN: I find new employees through the other people I have working on my team. The main thing I look for is that they are willing to work hard and care about doing a good job. I am less concerned whether or not they have experience with calves as I like to have the opportunity to train them from scratch so I can avoid any bad habits that may have come from previous employment.
If you employ a person without previous calf raising experience, how do you train them?
RACHEL: Employees start off with our on-boarding program where they will get a minimum of two weeks training.
MEGAN: I rely on my other team members that have been here the longest to train new employees. I have a lot of confidence in the group of people I have trained to make sure that the new people are properly trained. They know the standards to which we raise our calves and keep the others held to that standard. They also know that it will come back to them as well as make their job more difficult if they do not do a good job training the new people.
Do you use job descriptions or protocols in any way to assure that employees understand their specific duties, or do you employ a learn-as-you-go model?
RACHEL: We have job descriptions for our employees and written protocols for our employees to follow along with holding yearly trainings.
MEGAN: We have treatment and cleaning protocols that are in place on our farm. We try to keep things very consistent and as routine as possible so that there are never any questions as to how things should be done.
How do you keep the communication between yourself and team members open and ongoing?
RACHEL: We have lots of meetings! We like to meet and go over things before we start each day, then we also have monthly vet and staff meetings to review how things are going or any concerns.
MEGAN: I am working with my team every day and will jump in to help them from time to time. I believe that this helps them know that I don’t consider myself higher than them and during this time we can talk about anything that might need to be fixed or changed. If we are ever having problems with the calves, I will ask their opinion as to what is going wrong to see if they are noticing something I am not.
How do you balance the need to cross-train, in case team members need to cover for one another, with getting the normal daily work completed?
RACHEL: We believe you should always have three people trained to every job in case one is on vacation, one calls in sick or has an emergency, then you still have one person to rely on.
MEGAN: The calf team all knows how to do any of the jobs that would be required of them when it comes to things like bedding, feeding and cleaning. I have one person that is trained to treat and vaccinate calves when I am not there. For training, I had my protocols translated to Spanish and then had him work alongside me as I was doing the treating and vaccinating for a few weeks. We still will do this every once in a while, and ask questions, just to make sure he is confident in what he is doing and handling these situations.
How do you address any calf health or management issues that arise?
RACHEL: We have monthly vet meetings where we sit down and talk about all the positives and negatives happening within the calf department. We like to focus on the things we need to improve on before our next meeting.
MEGAN: When calf health issues arise, I check with my calf team to see if they have noticed anything that I haven’t. From there I do testing with our vet to find where the problem is. From there we work to make adjustments to make sure we do not run in to the same problem again.
How do you address on-going education and training of team members?
RACHEL: We have a yearly schedule of trainings that need to be reviewed and once a month we will check off those trainings as the year goes on. For example, sanitation training is due in September. We will make sure we set up a training date to review this with our teammates.
MEGAN: I work with my assistant calf manager a couple times a month to make sure we are on the same page.
Have you found any outside resources or websites particularly helpful in educating team members?
RACHEL: Lots of them! A few that came to mind are Cornell Cooperative Extension, Merck Animal Health and Zoetis.
MEGAN: I have not used outside resources to train.
Do you offer any incentives to your calf care team if certain goals are achieved (one example: average daily gain targets for x number of months each year)?
RACHEL: We have in the past, but we’ve stepped away from it for many reasons. If we could, we would! I think incentives are a creative way to help get employees engaged.
MEGAN: We do not have any incentives but I try to always make sure they know I appreciate the work they do. For example, if they worked really hard and got a lot done on a hot day, I will get them ice cream. I also like to get lunch for them once in a while when I notice that they have been working extra hard. I think small gestures like that go a long way to show appreciation for what they do for the farm.
What are three key things you would share with a first-time calf team manager?
RACHEL: Communication is key. Trust your employees. Inspire new ideas.
MEGAN: First, I would suggest finding a main go-to person on your team that you trust to take care of the calves when you are gone. You have to be gone at times and coming back to calves, that weren’t taken care of at the same level as you would, is not helping your calf program progress. Second, your team is going to put in as much as you do. Show them how important calf health is to you and they will make it a priority as well. Third, make sure you have protocols in place as this keeps everyone on the same page and gives something to fall back on when things are not getting done properly.
Kelly Driver, MBA has been involved in the New York dairy industry all her life. In addition to raising dairy calves and replacement heifers, she is the Eastern US & Canada Territory Manager for Calf-Tel. Feel free to contact her at kellydriver@hampelcorp.com with your calf questions or suggest a topic you would like addressed in a future blog.
Courtesy of our dealer – CRI REPRODUCCIÓN ANIMAL MÉXICO SA DE CV.